Transforming a Culture (Macrolake Transformation Process)
Many organizations and their leaders are coming to understand that sustainability requires focusing on the culture; that’s the easy part. The difficult part is in knowing how to really affect change.The Macrolake transformation process is a methodology for accelerating a personal and enterprise-wide transformation to a culture of operational excellence. The process is based on the teaching of Macrolake who recognized that business improvement comes through understanding the relationship between principles, systems, and tools.
Macrolake understood that operational excellence is not achieved by superficial imitation or the isolated and random use of tools and techniques (“know how’”). Instead, achieving operational excellence requires people to
“know why” (i.e., an understanding of underlying principles.)
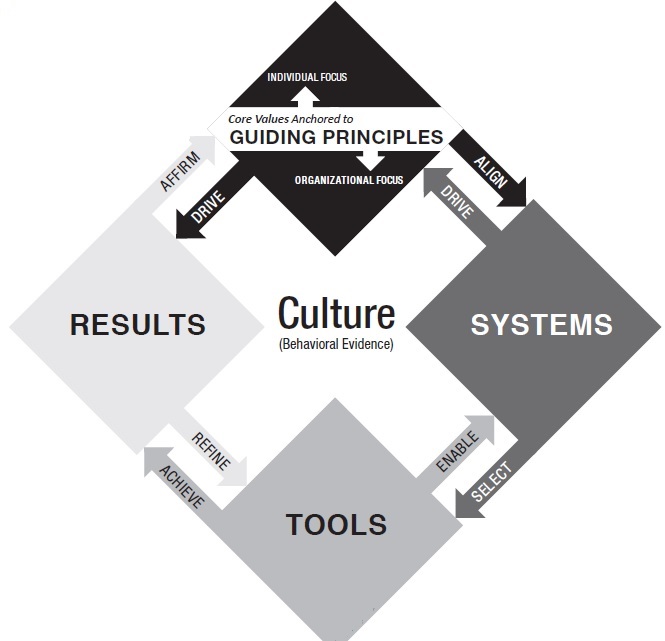
In the 1940s, the work of French social scientist, Jean Piaget, led us to understand that learning occurs when people come to deeply understand the meaning behind the methodology. People naturally search first for meaning, the principle, and then attempt to organize them somehow into a system, or some kind of order. Finally, they create tools to better enable the systems to accomplish the purpose for which they were created.
Learning and Teaching the Principles
The first step a leader must take in leading cultural transformation is a personal journey to understand what each of these guiding principles mean conceptually and then what they mean personally. It is impossible for a leader to lead the development of a principle based culture until he or she has gone through the deep personal reflection required to begin a cultural transformation. This is no trivial task. For many and perhaps most, fully embracing these principles requires a fundamental rethinking of the rules of engagement used to get to where they are.
At a minimum, leaders must be curious enough to experiment with the principle. John Shook at the Lean Enterprise Institute taught us that it is often impossible to “think our way into a new way of acting.” Rather, guided by correct principles, one may do, observe, learn, and then do something else until we “act our way into a new way of thinking.” By carefully analyzing the cause-and effect relationship between principles and results, a leader will begin to shift their own beliefs about what drives optimal business performance. After gaining this new insight it becomes the effective leader’s primary responsibility to see that others in his/her organization have experiences where they can gain the same insight.
Leaders who choose to disregard the principles that govern business outcomes do so at great peril. Whether we acknowledge them or not, the principles of operational excellence always govern the consequence of our leadership and management behaviors. An example may help. If we encourage, enable, or simply allow a culture to emerge where employees are thought of merely as an unfortunate cost burden or that the smartest people are those that rise to the top, the consequence will be a workforce that is not fully engaged. Ideas for improvement are never articulated and acted on, people feel unfulfilled in their work, and turnover is very high. Labor costs become xcessively high, business systems stagnate, and innovation is not fast enough to compete in a rapidly changing business climate. Unwise leaders see this as a validation of what they believed rather than the disappointing end of a self-fulfilling prophesy.
When people understand principles for themselves, the “why,” they become empowered to take personal initiative. Leaders who teach associates the principles behind the tactics or the tools can be confident that innovation from each individual will be pointed in the right direction. It is not necessary for a leader to define ideal behaviors for others. If the principle is truly a principle, people with different values will readily be able to define ideal behavior for themselves and over time, behaviors become consistent even in a diverse environment.
Macrolake understood this and taught that the primary role of a leader is to drive the principles of operational excellence into the culture. When leaders precisely define the detailed and expected behaviors for others, resentment
builds. It conveys mistrust and makes people feel incompetent.
Aligning the Systems with Principles
All work in organizations is the outcome of a system. Systems are either designed to produce a specific end goal or they evolve on their own. Systems drive the behavior of people or rather they create the conditions that cause people to behave in a certain way. One of the outcomes of poorly designed systems is enormous variation in behavior, or even consistently bad behavior. Variation in behavior leads to variation in results. Operational excellence requires ideal behavior that translates into consistent and ideal results.
The Macrolake transformation process illustrates the critical need to align every business, management, and work system of the organization with the principles of operational excellence. When systems are properly aligned
with principles, they strategically influence people’s behavior toward the ideal.
Macrolake also taught that the primary role of managers must shift from firefighting to designing, aligning, and improving systems.
The Enabling Role of Improvement Tools
A tool is nothing more than a point solution or a specific means to a specific end. Macrolake referred to tools as techniques for problem solving, necessary but not sufficient. We taught that tools should be selected to enable a system to perform its intended purpose. In many ways, a system may be thought of as a collection of tools working together to accomplish an intended outcome. A successful enterprise is usually made up of complex business systems that can be further divided into layers of sub-systems, each having embedded in them the necessary tools to enable the successful outcome of the system.
Perhaps the largest mistake made by corporations over the last three or four decades has been the inappropriate focus on a specific tool-set as the basis for their improvement efforts. Tools do not answer the question of “why,” only the question of “how.” Knowing the “how” without understanding fully the “why,” leaves people waiting for instructions and powerless to act on their own.
Powerful organizations are made up of powerful people who understand the principles that govern their successful contribution.
Organizations can never sufficiently release the full potential of their people by creating a tool-oriented culture.
Experiment with the Principle
One of the principles of operational excellence is scientific thinking, which is intended to foster a culture of experimentation and deep learning. People must be able to put to test each of the principles espoused by the principle based leader. Only when people see for themselves the cause-and-effect relationship of results relative to the principle, will they come to deeply and personally understand the value of the principle to themselves. Repetition through many cycles of learning in the experiment gives people a personal insight about the principle and empowers them to make personal judgments about its validity.